Organizace výrobní linky
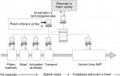
In-line (spřažená) výrobní linka
Prvním z nich je umístění všech technologií do jedné linky spojené dopravníky. Znamená to, že na vstupu linky jsou součástky, vstupní materiály a konstrukční prvky. Výstupem této linky je osazená deska plošného spoje (testovaná a bez nepřijatelných zbytků tavidla), v ideálním případě výstupním produktem je hotový a odzkoušený výrobek. Jednotlivá výrobní zařízení jsou pevně svázaná, kontrolována a řízena počítačem. Tento způsob vyžaduje přesné plánování výroby a je řízené z jednoho místa. Pro ostatní oddělení jako je: přejímka zboží a logistika, kontrola kvality materiálu, balení a doprava. Rovněž je třeba plánování materiálových nákladů a výrobní plánování. Plánování a řazení v továrně je založeno na odhadnutých dobách nutných k realizaci na každý výrobní krok. Objednávka položky začíná přejímkou zboží a postupuje od jednoho výrobního stupně k dalšímu. V továrnách s tradiční organizační strukturou je téměř nemožné identifikovat konečný produkt nebo kontrolou kvality.
Jakmile výroba objednávky započne, její jednotná kvalita, odhadnutá doba zpracování a kvalita výrobku se někdy zhorší v každém následujícím kroku. Zpětná kontrola výroby je náročná v organizaci, která nemá dokonale zmapované podmínky dílny. To předpokládá perfektně organizovaný výrobní tok: cyklus zpětné vazby může být příliš pomalý, protože chyby a odchylky jsou objeveny v rozpracované výrobě nebo až po dokončení. Tento způsob je vhodný pro výrobu jejíž výrobky mají jednotný charakter (přibližně technologie) a velké série.
Z výše uvedených skutečností vyplývá, že pružnost a efektivita takovéto linky může být rozdílná, proto je možné i jiné uspořádání. Dalším problémem pevného uspořádání zařízení v lince může být neplánovaná odstávka strojů. Menší efektivitu může způsobit i rozdílný výkon strojů.
Buňkové řazení výrobních technologií
Variantou výrobní linky může být i tzv. buňkové (hnízdové) řazení výrobních technologií. Menší nezávislé montážní jednotky jsou dobrým způsobem jak zvýšit výrobní pružnost a efektivitu jednotlivých zařízení a rovněž využít lidských zdrojů. Úkolem kontroly výroby vyžaduje, aby byly nejlépe využity zdroje: dodávky desek plošných spojů proběhly ve správný čas, v co nejlepší kvalitě a za minimální náklady, kvalita všech vstupních materiálů měla požadované parametry (např. doba zpracování pájecí pasty, atd). Kontrola výroby, která opravdu chce řídit tok výroby by měla znát současnou situaci a být schopna rychle zasáhnout a přizpůsobit zařízení požadavkům výroby.
Kontrolor by měl znát následující informace o výrobě:
- stav všech objednávek a rozpracované výroby,
- stav kvality výrobků a postupů,
- stav strojů a zařízení,
- personální situaci,
- stav použitelnosti materiálů.
Pokud tyto informace nejsou k dispozici, výroba nemůže být kvalitně řízena a zajištěna ve správném termínu. Moderní postupy výroby hledají hierarchické rozčlenění kontroly a snaží se přesunou více odpovědnosti na jednotlivé pracovní úrovně. Ideálně by se továrna skládala ze struktury nezávislých modelových jednotek nebo buněk. Tyto jednotky požadují dvě doplňující podmínky stejně jako celkovou odpovědnost za jejich vlastní zdroje. To jsou: nezávislost v podmínkách dodávek materiálů (v tomto případě dodávky součástek) a nezávislost v podmínkách řízení.
Nezávislost v podmínkách materiálů znamená, že pro každou součástku je na objednávce nezávislá inventura v místě použití. Požadavek na materiál začíná v konkrétní montážní buňce, spíše než v MRP. Nezávislost v podmínkách řízení znamená, že rozčlenění práce může být organizováno těmi požadovanými v konkrétní buňce. To dále znamená, že nereálné požadavky nebo výrobní objednávky mohou být kontrolovány z hlediska proveditelnosti a podle toho potvrzeny nebo zamítnuty. Obojí podmínky mohou být realizovány na požadavky určené organizací a hierarchickým informačním systémem s důrazem na dílenský informační vstup a postup výroby (obr. 1).
Systém je vyprojektován tak, aby řídil materiály takovými způsoby, které minimalizují nároky a výrobní čas. To optimalizuje množství používaných materiálů a jejich pozice – JIT praxe – v továrně. Hlavní linky logistiky byly:
- distribuce způsobená rostoucí poptávkou
- dodávky Kanban
- skladování součástek v krabicích v automatizovaném skladu s variabilním rozložením
- použití materiálů FIFO
- automatizovaná doprava
Výběr součástek pro výrobu je prováděn dvěma způsoby v závislosti na množství součástek v krabici vzaté ze skladu. Pokud je zde méně než vyžaduje Kanban paměť, systém předsune neporušenou krabici, jinak operátor vybere požadované množství. Systémová kontrola je založena na počítačové síti. Koncentrátor - počítač řídí požadavky skladu (obdržené zboží a materiály a jejich následující distribuce). Tato počítačová síť logistiky je vedena na počítač vyšší úrovně, který přenáší informace obsahující objednávku výroby a materiálové zásoby. To je poté napojeno na počítačovou síť výroby za účelem přenést požadavky Kanban a na nižší úrovni řídit výrobně strojní počítače.
Výrobní plocha je rozdělena do jednotlivých toků vyhrazených daným kategoriím DPS. Montáž desek a testování je založeno na následujícím:
- Linky rozdělené do tří nebo čtyř “krátkých buněk” (tj. automatické vložení buňky).
- Buňka konečné montáže & pájení a testovací buňka.
- Nastavení nulového času (tj. žádné ztrátový čas při výměně materiálu nebo kontroly programů).
- Kompletní sledování DPS.
- Bezpapírová metodologie.
- Automatizovaná doprava.
- Sledování údajů o kvalitě na každém výrobním kroku.
Každá linka je konfigurována jako nepřetržitý proces, který je rozdělen do různých buněk za účelem redukce složitosti na jednoduchou instalaci a zvýšit pružnost umožňující opětovné řízení procesu do jiných linek za přidělenou buňku. Pohyb desek v buňce probíhá dopravníky vybavenými automatickým nastavením šířky. Mezi buňkami jsou desky sebrány do policového zásobníku a transportovány laserovými nosiči. Díky svému designu jsou skladovací jednotky nazývány portálové nárazníky, které skladují nebo vyskladňují desky během výrobního procesu k vyrovnání asynchronních operací buněk (tj. když je jedna buňka mimo krok jiné).
Ostatní buňky řídí umístění a vkládání strojů. Pro výrobky SMT zahrnují buňky umístění strojů, sítotisku a pece. Existují dva typy: jeden pro montáž horem a jeden pro montáž spodem.
Konečné vložení součástky, vizuální kontrola a pájení vlnou jsou provedeny v buňce konečné montáže. Testovací buňka používá “in-circuit” tester nebo jiné funkční testovací zařízení. Opravné operace jsou dodávané softwarem (Siemens - SICALIS QME pouzdra). Tento software překládá výsledky testu a řídí video terminály na opravných stanicích. Obsluha může opravit DPS pomocí postupů řízených softwarem. Software je použit na všech částech linky ke sběru dat.
Systémy kontroly kvality zahrnující elektronickou výrobu musí zajistit, aby chyby nebo omyly v umístění, pájení a ostatních činnostech montáže byly objeveny a opraveny. Výrobní linky Italtel používají integrované schéma určené SICALIS QME. SICALIS je pomocný počítač, systém kontroly kvality na úrovni továrny.
V Carini jsou instalovány za každým výrobním krokem body vizuální kontroly tak, aby garantovaly rychlou zpětnou vazbu během náhlé poruchy nebo chyby. Pracovní místa jsou vybavena grafickými terminály, které ukazují reálné schéma a data odvozená přímo ze systému CAD. Součástka, pájení a chyby umístění mohou být identifikovány strukturovaným způsobem jednoduše kliknutím myši. Pro snazší rozhodnutí, zda je součástka OK nebo není OK, jsou na displeji zobrazeny také obrázky typických chyb.
Možná nejzajímavější část systému kvality je vyhodnocovací nástroj založený na relační databázi, která obsahuje kompletní historii desky. Databáze má informaci o objednávce, každý stroj, který prošel, a každou chybu objevenou a opravenou na jednotlivých DPS. Databáze není jenom základní nástroj pro posouzení v souladu s řadou ISO 9000, ale také jedinečná příležitost vyzkoušet vývoj současného strojírenství a souvislého výrobku. Např. jisté SMD ukázaly 400krát vyšší rozsah chyb, když byly umístěny na té straně pro pájení vlnou než když byly umístěny na horní straně DPS. Tento výsledek vyžaduje nový design některých výrobků a určuje pravidla designu pro rozvoj.
Investice do nových výrobních kapacit by měla být cílem redukce doby zpracování, zlepšení postupů a zvýšení kvality. Malé a nezávislé výrobní buňky, které zahrnují lidské zdroje pro řízení procesů se ukázaly jako splňující tyto podmínky. V továrnách s tradiční organizační strukturou je vliv a odpovědnost kompletně z dosahu: obsluha je příliš závislá na kvalitě a dodávkách procesního řetězce. Navíc, jejich pokusy se stávají mnohem více “požadovanými” a mohou být mařeny rozhodnutím vyšší úrovně, jenž bylo vydáno výrobním plánováním a řízením pomocného počítače, který všeobecně není schopen vzít v úvahu podmínky dílen. Nová koncepce jako ta instalovaná v Carini umožňuje nezávisle zavést v buňkovém výrobním prostředí.
Praktické informace získáte na školení Zásady SMT výroby
► Nákup na www.abetec.cz
► Další odborné články
► e-Shopy, školení a e-Booky
![]() |
![]() soldering.cz |
![]() e Booky ZDARMA |
![]() fotografie |
![]() video |